在工業制造領域,產品質量與可靠性至關重要。大型冷熱沖擊箱作為模擬溫度環境的關鍵設備,在物理測試中發揮著不可替代的作用。而隨著工業 4.0 時代的來臨,其可靠性評估也正經歷著深刻變革。
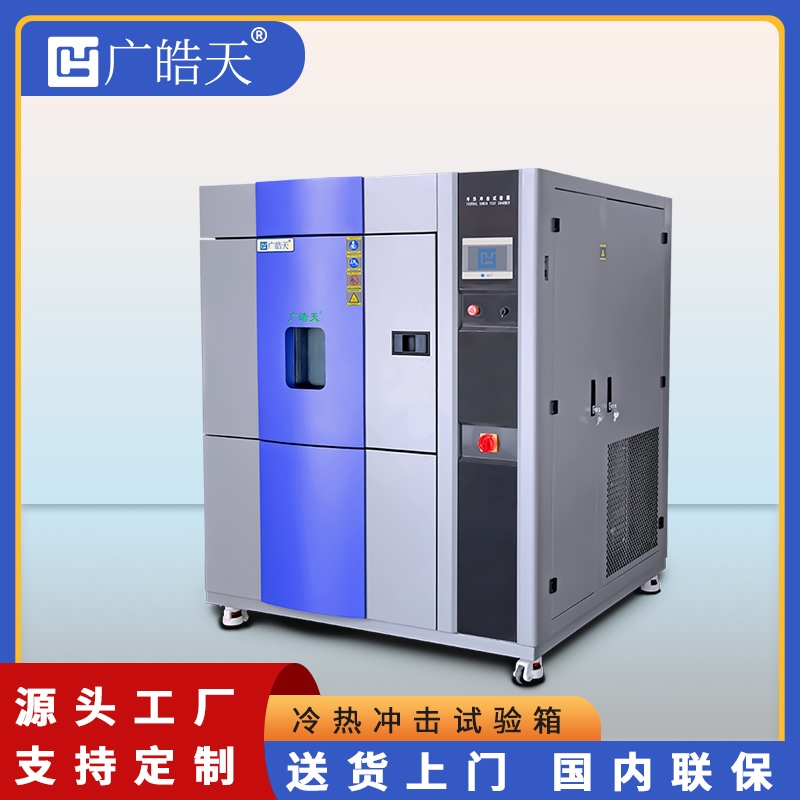
大型冷熱沖擊箱通過快速切換高溫與低溫環境,對產品進行嚴苛考驗。例如在電子設備制造中,將電子產品置于箱內,從高溫 150℃迅速切換至低溫 - 60℃,在這一過程中,檢測電子元件的焊點是否會因熱脹冷縮而開裂、電路板是否會變形等。像某手機廠商利用此類設備測試充電接口,發現 - 40℃低溫下金屬觸點易脆斷,進而改進設計提升了產品良率。又比如汽車制造,模擬車燈從寒冷雪山到炎熱沙漠的環境變化,測試車燈塑料件是否變形、密封膠是否失效,以此確保汽車零部件在復雜環境下的可靠性。 當下,大型冷熱沖擊箱物理測試已廣泛應用于各行業。然而,傳統測試面臨一些挑戰。一方面,測試數據的采集與分析多依賴人工,效率低且易出錯。例如,在記錄產品性能參數變化時,人工記錄可能出現遺漏或偏差。另一方面,測試場景相對單一,難以全面模擬現實中復雜多變的環境。如在一些特殊工業場景中,除了溫度變化,還存在濕度、振動等多種因素共同作用,傳統測試難以兼顧。
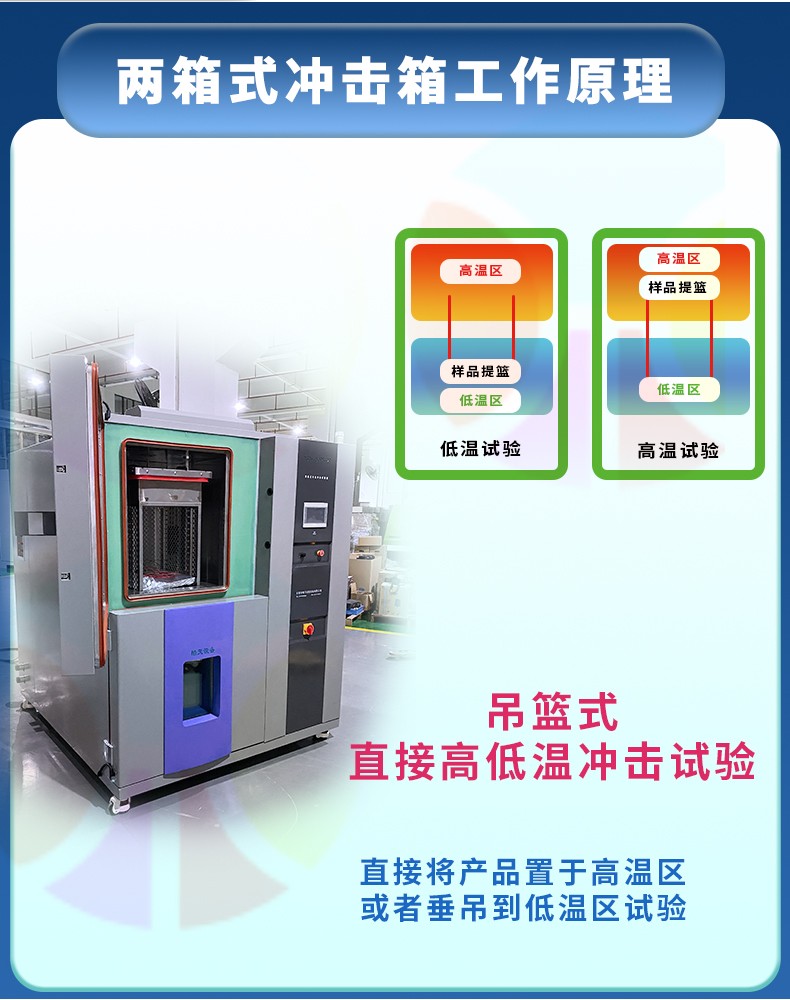
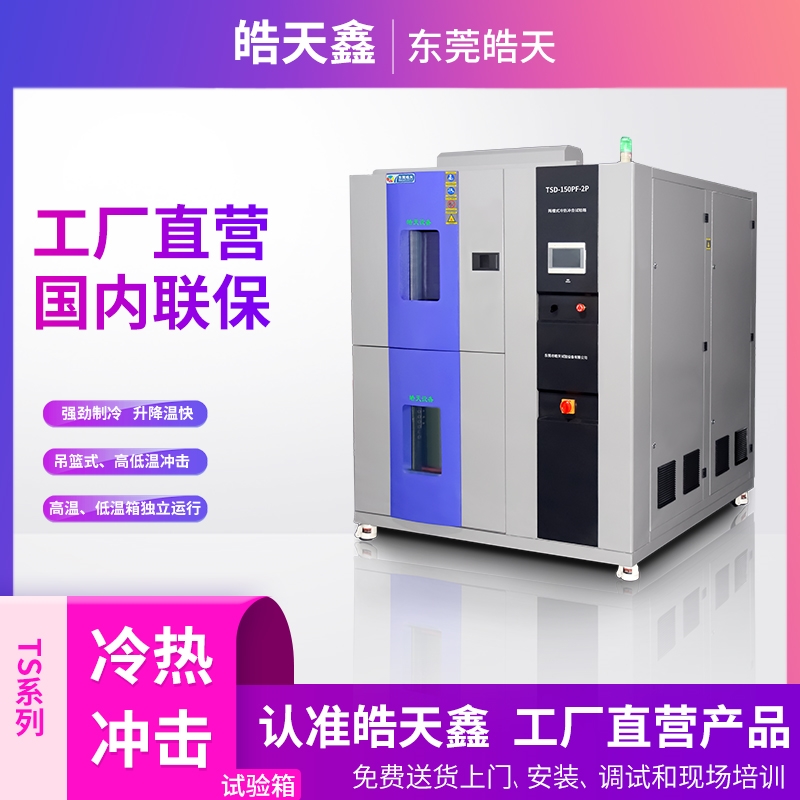
進入工業 4.0 時代,可靠性評估迎來新契機。借助工業物聯網(IIoT)技術,大型冷熱沖擊箱可與其他設備互聯互通,實時采集大量測試數據。通過對這些數據的深度挖掘與分析,企業能更精準地把握產品在不同溫度沖擊下的性能變化趨勢。比如,利用大數據分析技術,可預測產品在未來特定環境下可能出現的故障,實現從 “事后補救” 到 “未卜先知” 的轉變。
數字孿生技術也為可靠性評估注入新活力。它能構建與實體產品相對應的虛擬模型,基于測試數據實時更新模型狀態。以某航空發動機零部件測試為例,通過數字孿生模型,工程師可直觀觀察到零部件在冷熱沖擊過程中的內部應力變化,提前發現潛在問題,優化產品設計,大大縮短研發周期。
在工業 4.0 浪潮下,大型冷熱沖擊箱物理測試正朝著智能化、精準化方向邁進,其可靠性評估的變革將有力推動各行業產品質量提升,助力工業制造向更高水平發展。